AIM Delivers Enterprise Wide EDI, Inventory Control and Industry 4.0 Mobile App Solutions to Dajaco Industries, Inc.
- Automotive supplier worked with AIM to implement AIM’s EDI solution, material control solution and Industry 4.0 shop floor technologies
- AIM Computer Solutions implemented the AIM Vision EDI, Bar Code Labeling, Shipping and Receiving modules, commonly referred to as AIM AutoSys, to meet the EDI and labeling needs of this growing automotive supplier
- The company’s inventory accuracy consistently falls in the 98-99% range
- Dajaco’s Industry 4.0 technologies now include AIM mobility apps
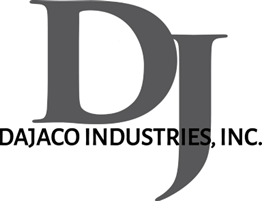
Three Needs: EDI, Inventory Accuracy and Mobility Apps
AIM Computer Solutions has worked with Dajaco Industries for more than two decades as their needs evolved. As the company has grown, it implemented AIM Vision EDI in 1998, integrated AIM’s material control solution in 2009, and added Industry 4.0 AIM Mobility apps in 2018. As the automotive supplier in the metal stamping industry streamlines its operations, it has looked to the future and updated its processes.
EDI Challenge
Dajaco Industries, Inc., a full-service automotive supplier of high-quality metal stampings and assemblies, required a top-notch, end-to-end EDI solution to meet automotive OEM and tier supplier requirements. Back in the 1998, they had staff members who wrote their own program in BASIC to process shipping, receiving and inventory. However, when it came to developing programs to support the EDI functionality, they struggled to tie the complex EDI requirements to their programming language. They needed to find a better solution in order to meet the requirements of an automotive industry supplier.
EDI Solution
The company implemented the AIM Vision EDI, Bar Code Labeling, Shipping and Receiving modules, commonly referred to as AutoSys, to meet its EDI and labeling needs.
The AIM Vision modular-based ERP solution embeds business logic for more than 450 OEM and sub-tier trading partners with more than 1,800 AIAG standardized bar code label formats. The solution’s EDI and supply chain logic manages the import of goods, schedules their arrival and accounts for their delivery against multiple customer releases. Now users set parameters to optimize document processing based on trading partner business logic and specs. AIM Vision automates the management of CUMs, ASNs, all releases and changing forecasts – the company gains full coordination of orders, releases, and forecasts.
EDI Results
Implementing AIM AutoSys provided them with an EDI, inventory and shipping system all in one solution. “As we established EDI trading partner relationships and on-boarded each customer’s EDI requirements, we were able to set it and forget it,” said Jim Ureel Jr., President of Dajaco Industries. “AIM was an all-in-one deal for us—we were able to improve our shipping and receiving capabilities, as well as meet our EDI requirements.”
Inventory Accuracy Challenge
To make informed decisions and plan for a competitive future, Dajaco Industries looked to improve its inventory control and operations. People were manually entering production tickets and getting parts and quantity wrong. Sometimes tickets were not entered daily, which led to misinformation and inventory inaccuracies. To optimize inventory accuracy and transparency, Dajaco wanted a reliable material control solution that integrated with their existing AIM AutoSys solution.
Inventory Accuracy Solution
With the AIM Vision Inventory and Production solution, Dajaco Industries now has the 21st century tools it needs for inventory reliability and transparency, resulting in better decision making and forecasting. Using AIM’s EDI bar codes and labels, Dajaco Industries gains complete real-time inventory tracking and traceability required by the automotive industry. Inventory counts are now more efficient and accurate. Production and delivery schedules are more reliable, leading to greater customer satisfaction. The company now tracks inventory transactions via an audit log, parts balances and various time-sensitive reports to optimize traceability.
Inventory Accuracy Results
Dajaco started using AIM Vision to manage Part Routings and BOMs. “Once we started this, everything fell together,” says Jim Ureel, Jr. Dajaco takes a physical inventory count, and has been able to maintain superior inventory accuracy levels.
“Before AIM, we didn’t really have inventory control, we were guessing at everything. Now with AIM Vision, we have better inventory control, we know what we have, where it is, which warehouse it is in; I’d have to say it’s about 98-99% accurate,” expressed, Jim Ureel, Jr.
Once inventory is correct, Dajaco Industries can focus on scheduling and utilizing the MRP and CRP features in AIM Vision.
Industry 4.0 Technologies Adoption Challenge
Wisely looking to the future of digital transformation, Dajaco Industries selected Industry 4.0 technologies to further streamline its shop floor operations. It specifically wanted improvements in visibility of jobs and machines, and to increase efficiency on the shop floor by utilizing tablets and mobile apps to perform daily receiving, production and shipping tasks.
Industry 4.0 Technology Adoption Solution
Dajaco Industries positioned itself as an Industry 4.0 early adopter using AIM Mobility apps. The apps promote real-time plant-floor intelligence via easy-to-use hand-held scanners and tablets.
AIM Mobility Receiving was implemented to scan vendor labels at the receiving dock instead of entering manual receipts, saving time and reducing data input errors.
AIM Mobility Shipping was implemented to scan customer compliant labels of staged shipments at the shipping dock, verifying and matching the ship order, then print shipping paperwork directly from the tablet.
Scheduling the plants is now done via the AIM Digital Whiteboard. Upon initializing the whiteboard, of which Dajaco may choose to have many, the whiteboard displays machines and jobs in tile format. “This is a real time-saver. It tells us what to run, where to run it, and how many to run,” says Jim Ureel, Jr. “And in our hand assembly area, where PPAP is not an issue, we are able to drag and drop jobs to different work centers to help balance the workload.”
The most recent Industry 4.0 implementation was the AIM Mobility MES App. This app automates production tracking and reporting from the shop floor, increasing operator efficiency, and reducing operator time to label product. Shift supervisors or operators use the Digital Whiteboard schedule to load jobs to a work center. The operator then logs in to the work center and runs production. The AIM Mobility MES app tracks material used, machine downtime, scrap reporting and labor efficiency.
Industry 4.0 Technology Adoption Results
The company implemented several AIM mobility apps to improve operator productivity and efficiency, increase inventory accuracy, and increase factory capacity utilization.
Dajaco Industries has adopted the Digital Whiteboard and AIM Mobility MES App into all of its plants. “These technologies are incredibly flexible,” commented Jim Ureel. “We have implemented it in our WIP and finished goods plants with a tablet and printer at every work center. The operators post real-time production at the machine, and print WIP traveler labels or finished goods customer compliant labels before the tote is carried away from the machine. In our prototype plant, where we have 30 machines, we have two tablets set to run the AIM Mobility MES App. We simply set the work center to match the machine we are running prototype parts on today, and we are good to go.”
Now the company is well poised to meet future demand and grow as a world-class automotive manufacturer of quality metal stampings and assemblies.
Conclusion
AIM Vision and AIM Computer Solutions mobility apps give automotive suppliers the tools to address ongoing challenges. AIM grows with you as your company grows.
Download a printable copy of the Dajaco Industries, Inc. Customer Success Story here.